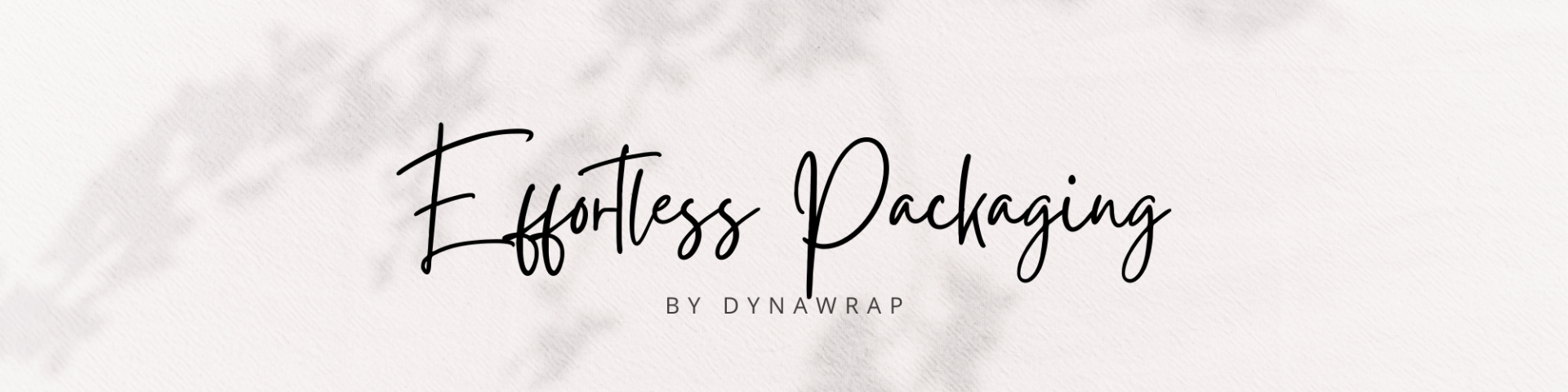
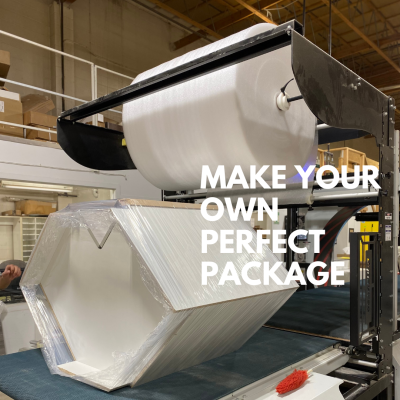
Exploring More Economical Solutions
Stretch Film Wrapping:
For most cabinetry and door manufacturers, stretch film wrapping emerges as the preferred end-line packaging solution. It offers several advantages, including wider availability and cost-effectiveness compared to other methods. Manual stretch wrapping is popular among small and medium manufacturers due to its ease of use. Many larger manufacturers integrate an Orbital Wrapping Machine into their end line, increasing productivity and ensuring consistent packaging quality.
In some cases, stretch film protection alone may not be sufficient, prompting the addition of a foam sheet or air bubble layer before applying the stretch film. Combining air bubble protection with stretch film wrapping provides the highest level of packaging safety against damages, humidity, and water.
By incorporating a horizontal wrapping machine into your end line, not only can you boost production speed, but you also gain a versatile packaging line. Furthermore, a well-built machine reduces labor costs, while adhering to standard packaging levels ensures high-quality products and customer satisfaction.
Efforthless Packaging For Cabinetry Manufacturers
Introduction:
As a cabinetry manufacturer, finding the best packaging solution for your products is crucial to ensure they reach your customers in pristine condition. The packaging method you choose depends on what you are packing and your production goals. In this article, we will explore and compare three available options: corrugated cardboard, shrink wrap machines, and stretch film wrapping, to help you make an informed decision for your business.
Corrugated Cardboard:
Corrugated board packing is a common choice, especially for products with specific dimensions or when customers prefer it. However, it is the most expensive option due to the higher cost of paper compared to plastic or stretch film. The need to use larger quantities of board can drive packaging costs up to three times more. Additionally, the lack of stretch film may cause products to shift inside the box during transit, potentially leading to surface damage.
Drawbacks of Hot Packaging
Shrink Wrap Machine Packing or Hot Packaging:
Shrink wrapping is favored by medium to large manufacturers as it provides protection against scratches and offers an alternative to corrugated cardboard. While it requires an initial investment in the machine, it proves cost-effective in the long run. However, the packaging speed may become a bottleneck for cabinet makers with high-speed production needs. Moreover, certain products may not be suitable for heat exposure, and changing product dimensions may necessitate different-sized reels, causing downtime on the packaging line. The continuous heating required by the shrink tunnel also leads to higher electricity consumption and increased operational costs.
Conclusion:
Choosing the right packaging solution is essential for cabinetry manufacturers seeking to protect their products during shipment and storage. While corrugated cardboard, shrink wrap machines, and stretch film wrapping each have their advantages and disadvantages, many manufacturers prefer stretch film wrapping due to its cost-effectiveness, availability, and ease of use. For added protection, combining air bubble layers with stretch film proves to be the safest option. Integrating a horizontal wrapping machine into your production line not only increases efficiency but also ensures consistent packaging quality. Selecting the optimal packaging method will not only safeguard your products but also enhance your customer's satisfaction and trust in your brand.